KEY ENERGY METALS APPLICATIONS FOR POWER GENERATION
Power generation provides electricity for homes, businesses, and infrastructure. Key energy sources include fossil fuels, nuclear power, and renewable energy.
Power generation facilities operate in diverse and often harsh environments. Power plants, whether coal-fired, natural gas, nuclear, or renewable, are exposed to extreme temperatures, high pressures, and corrosive substances. These challenging conditions necessitate using robust, high-performance materials, including exotic and refractory metals, to ensure the longevity and efficiency of energy generation systems.
Here are some of the top applications and metals used.
Energy
Industry
Sectors
Where Refractory and Exotic Metals Fit Into Energy Industry Sectors
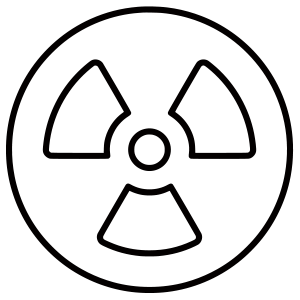
Nuclear Reactor Components
Nuclear reactors are vital in the energy industry. They provide a reliable and significant source of low-carbon electricity, can produce a steady and substantial amount of energy regardless of weather conditions, and help to reduce greenhouse gas emissions, contributing to efforts to combat climate change. Key nuclear reactor components include experimental fusion reactors, ion colliders, separators, radiation shields, heat shields, and control rods.
Special precautions are needed for operational safety and environmental protection. Nuclear reactor components must maintain structural integrity and resist long-term degradation to prevent failures and radiation leaks.
To withstand the extreme temperatures, intense radiation, and corrosive environments characteristic of nuclear reactor applications, the components require the high-temperature stability and radiation resistance inherent in refractory metals, particularly Tungsten, Molybdenum, Zirconium, and Niobium.
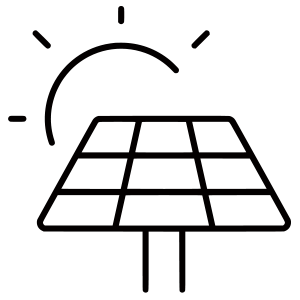
Renewable Energy Systems
Renewable energy systems harness natural resources such as sunlight, wind, water, and geothermal heat to generate electricity and provide sustainable power solutions, including solar panels, wind turbines, hydroelectric dams, and geothermal plants. The energy industry increasingly focuses on renewable energy systems, which are essential for reducing greenhouse gas emissions and promoting a cleaner, more sustainable energy future.
Despite their inherent sustainability, these systems are exposed to various environmental conditions, such as extreme weather, temperature fluctuations, and corrosive elements.
Specialized metals, including Titanium, Tungsten, Molybdenum, and Nickel alloys enhance the efficiency and durability of renewable energy systems by providing the necessary strength and resistance to harsh environmental conditions. For instance, Titanium is sometimes used in the blades due to its exceptional strength-to-weight ratio and resistance to fatigue and corrosion.
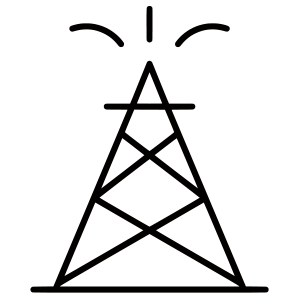
Oil & Gas Drilling Equipment
Oil and gas are critical to the energy industry due to their high energy density, reliability, and established infrastructure. They are primary energy sources for transportation, electricity generation, and industrial processes, providing a consistent and large-scale power supply. These naturally occurring hydrocarbons formed by heat and pressure over millions of years are found in deposits worldwide and extracted through drilling operations.
Drilling equipment operates in some of the most demanding environments, including deep underground and offshore ocean locations where high pressures, extreme temperatures, and corrosive substances are common. Drilling equipment in the energy industry requires specialty metals with exceptional strength, durability, and resistance to corrosion and wear.
Metals like Nickel alloys and Titanium can withstand these challenging conditions, ensuring the reliability and longevity of the drilling equipment while minimizing downtime and maintenance costs.
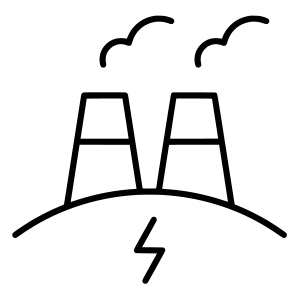
Fossil Fuel Power Plants
Fossil fuel power plants, which include coal, natural gas, and oil-fired plants, are critical components of the global energy industry infrastructure. These plants burn fossil fuels to generate steam, which drives turbines to produce electricity.
The environments within these power plants are extremely harsh and characterized by high temperatures, high pressures, corrosive gases, and particulate matter. The combustion process generates intense heat, requiring materials that can withstand temperatures often exceeding 1000°C (1832°F). Additionally, components in these plants must endure thermal cycling, mechanical stress, and exposure to aggressive chemical environments.
To meet these demanding conditions, fossil fuel power plants rely on refractory and exotic metals known for their exceptional heat resistance, mechanical strength, and corrosion resistance. Nickel alloys and Molybdenum are prevalent in fossil fuel applications, including boilers, turbine blades, and combustion chambers.
Industry Standards and Requirements
Industries constantly evolve, driven by a growing demand for scientific and technological advancement. Successful experimentation must ensure material integrity, safety, performance, and compliance with strict environmental and operational regulations.
These standards typically focus on aspects like purity, quality, and durability to guarantee that refractory metals meet the demanding conditions of high-stakes research applications. Because they serve multiple industries and extreme environments, this list includes more than average standards and requirements.
Standards and Requirements:
- ASTM International (American Society of Mechanical Engineers): Standards for materials used in energy applications.
- SAE Aerospace Material Specifications (AMS, formerly known as the Society of Automotive Engineers or SAE)
- ASME BPVC (Boiler and Pressure Vessel Code): Guidelines for materials used in pressure vessels and reactors.
- Department of Defense (DoD) Military Standards or Military Specifications (MIL) on the Defense Logistics Agency (DLA) ASSIST Database
We adhere to quality compliance certification standards and statutory regulations that pertain to our exotic materials, processes, custom machining services, traceability, and other aspects of our in-house expertise. Our materials specialists provide expert counsel on metal selection and inspection to ensure you receive materials that meet or exceed your expectations.
Leading Edge Metals & Alloys Certifications include:
- ISO9001:2015 and AS9100D Registered
- ITAR Registered
- NIST SP 800-171 and CMMC Compliant
Our deep understanding of this industry stems from our extensive experience, skilled metallurgy professionals, and a history of successful partnerships with leading national research labs.
The Bottom Line on Metals in the Energy Industry
The energy industry requires specialized materials that can withstand extreme conditions, from high temperatures in nuclear reactors to corrosive environments in oil and gas extraction. At Leading Edge Metals & Alloys, we understand the unique needs of the energy sector and provide a wide range of exotic and refractory metals tailored to meet these demands.
Why the Energy Industry Buys Rare and Exotic Metals
- Durability: High resistance to wear and corrosion extends the lifespan of components.
- Efficiency: High-performance metals improve energy conversion and reduce losses.
- Safety: Robust materials ensure operational safety in extreme conditions.
Key Energy Metals We Offer
- Tungsten: Excellent for high-density applications like radiation shields and counterweights, with exceptional heat resistance ideal for nuclear applications. Explore Tungsten
- Niobium: Exceptional superconducting properties, especially at low temperatures, are ideal for ion colliders in nuclear reactor applications. Explore Niobium
- Molybdenum: High strength and thermal conductivity, perfect for energy generation. Explore Molybdenum
- Zirconium: Excellent corrosion resistance, used extensively in nuclear reactors and chemical processing. Explore Zirconium
- Titanium: Exceptional strength-to-weight ratio and resistance to fatigue and corrosion, used in wind turbine blades and offshore environments. Explore Titanium
- Nickel Alloys: Superior corrosion resistance for oil and gas environments. Explore Nickel Alloys