Nuclear Fusion Reactor Innovation
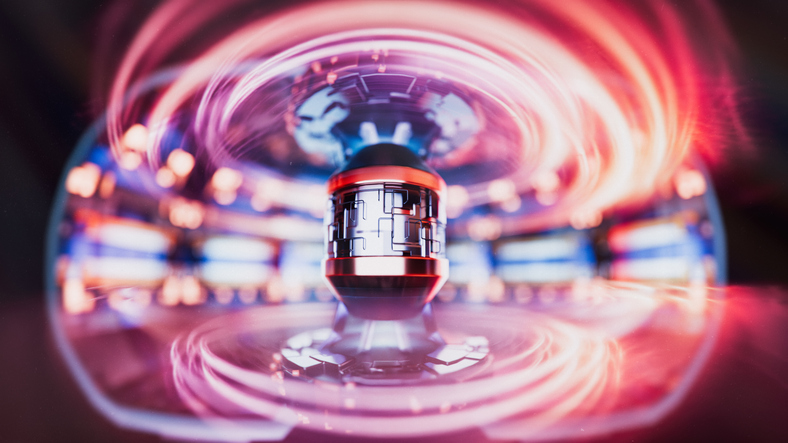
Refractory Materials and Nuclear Fusion
Long-researched by scientists worldwide, the nuclear fusion reactor promises a sustainable, carbon-free energy source with minimal radioactive waste. However, achieving the extreme conditions necessary for a self-sustaining reaction remains a massive scientific and engineering challenge. With specialized knowledge, capabilities, and innovative spirit, we’re all in on contributing to the solution and harnessing the opportunities of nuclear fusion for generations to come.
What is a Nuclear Fusion Reactor?
Before we talk about what nuclear fusion is, we first must touch on what is not. In general, when people refer to the current technology of nuclear reactors or nuclear energy, they are talking about nuclear fission, in which the nucleus of a heavy atom is split into two smaller nuclei, some neutrons, and a huge amount of energy. The released neutrons trigger further fission in nearby atoms, creating a chain reaction. Nuclear fission is commonly and broadly used to produce nuclear energy. While fission generates significant amounts of clean energy, it also produces radioactive waste, which requires careful management and oversight.
Nuclear fusion, on the other hand, is a high-potential process that is still emerging through extensive research and development. It can provide a nearly limitless, clean, and safe energy source. That’s because, unlike nuclear fission, nuclear fusion produces only minimal waste. It’s inherently safer than fission, but it requires extreme conditions, including temperatures reaching millions of degrees. Researchers are still working on cracking the code to achieve a stable, self-sustaining nuclear fusion reactor that produces more energy than it consumes, and spoiler alert – we’re helping them!
In nuclear fusion, two light atomic nuclei combine to form a heavier nucleus, releasing a large amount of energy. A nuclear fusion reactor is a device that aims to generate energy by fusing atomic nuclei under extreme conditions of heat and pressure, similar to those found in the Sun and stars. The most common reactor design is a tokamak, which uses powerful magnetic fields to contain and manage the extremely high-temperature plasma the process requires. After decades of research, scientists are still working to solve the challenge of sustained plasma containment to keep it from touching the reactor walls.
What does this have to do with refractory metals and the experts who process them through custom machining capabilities? The answer is more than you might think.
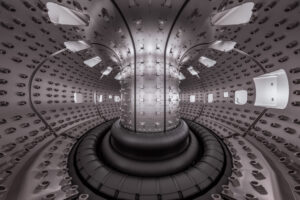
3D rendering nuclear fusion reactor
The Special Role of Exotic and Refractory Metals in Nuclear Fusion
As you might guess, exotic and refractory metals are key materials in a nuclear fusion reactor thanks to their ability to withstand extremely high heat. In particular, pure Tungsten has the highest melting point and tensile strength of all metals, making it essential for use in nuclear fusion. We supply Tungsten, but it’s our expertise in metallurgy and machining that has made us a go-to partner for nuclear fusion researchers and national labs.
Machining and Process Innovation for the Fusion Reactor
Pure Tungsten comes in sintered and rolled plates, and the properties that make it ideal also make it difficult to produce and machine. As we worked with the researchers, we realized there were ways to apply our expertise beyond simply supplying the materials for this highly specialized and experimental application with incredibly tight tolerances.
Working collaboratively with our chief metallurgist Bob Desberg, and channel partners, including Commonwealth Fusion Systems, Massachusetts Institute of Technology (MIT), Oak Ridge National Laboratory, and an approved machine shop in our network, we identified critical elements of innovation that have the potential to change the game when it’s time to scale production. Here are a few of our areas of high-impact innovation:
Cutting/Machining
Our custom machine shop uses a water jet to cut the Tungsten rolled plate into the proper blank size before they go to our channel partner for full machining and component production and then return to us for additional processing steps.
Traceability/Documentation
One of the critical steps in this process is documentation for traceability. This is crucial in nuclear fusion reactor production to ensure:
- Material Quality and Integrity
- Safety and Accountability
- Regulatory Compliance
- Maintenance
Traceability is necessary at the individual component level in each nuclear fusion reactor, which means each piece of Tungsten must have a unique serial number. That’s a machining project in and of itself – not only to machine 22,000 parts but also to provide documentation for traceability for each part. It required significant innovation on our part to develop the meticulous process. Let’s just say the paperwork could possibly weigh more than the metals when it’s all said and done.
QA/Inspection
With tolerances so tight they’re nearly impossible to achieve, there is no room for error in the nuclear fusion process. Even the inspection procedures for quality assurance (QA) needed to be reinvented. That includes who, what, when, where, and how to complete the QA for full confidence in the final product.
Cleaning and Packaging
When purity and performance are at stake in such extreme conditions, component and equipment cleanliness is essential. The tiniest impurity or trace contamination in the nuclear fusion reactor can affect performance and even lead to corrosion, degradation, or failure. We developed a dedicated clean room and protocols to address this critical element.
Project Management
Order of operations and oversight matters. There are many players and many steps that have to come together seamlessly and flawlessly in these research and production processes. Our team is proud to have injected expertise and innovation at every step through meticulous project management, and we’re not finished yet.
The State of Fusion Reactor Research and What’s Next
We’ve come a long way toward turning the dream of a market-viable, scalable nuclear fusion reactor into a reality, but there is still a long way to go. Everything we’ve discussed is at the prototype stage, where researchers are working to prove the technology is possible. Once that happens, the real fun starts – scaling up by multiples in both size and production volume.
The metals we are sourcing, and the components we manufacture are small but essential pieces of the giant puzzle. Even more important and impactful is our successful innovation of the entire process. We are poised to continue scaling up as a global partner for clean fusion energy, research, and national labs, as well as other complex industries we serve, including aerospace and defense, medical, and electronics.
Contact us to discuss nuclear fusion and other exotic and refractory material applications, or request a quote to cut right to the chase. Sign up to receive our monthly newsletter, and join the conversation on LinkedIn.